Understanding Contract Costing in Cost Accounting
Thu May 08 2025Contract costing in Cost Accounting is primarily used in construction and engineering projects, where costs are tracked and analysed for each contract. It involves detailed accounting of direct and indirect costs and revenues over the life of a contract, which often includes features like progress billing and escalation Clauses to manage large-scale, long-term projects effectively. Control costing is a specialised form of job costing, which is typically used in industries where work is undertaken on a contract basis, such as construction, shipbuilding, and large engineering projects. Each contract is treated as a unique cost unit, with costs and revenues explicitly tracked for that contract. For instance, in building a bridge, a contract costing would involve detailed tracking of all costs and revenues tracked for that contract. For instance, in building a bridge, contract costing would involve detailed tracking of all costs (material, labor, subcontracting) related to that specific bridge project, differentiating it from other projects the company undertakes. Enhances your financial expertise with comprehensive Cost Accounting courses covering key concepts.
What is Contract Costing?
Contract costing is an accounting method used for big projects like construction. It's used when a contractor agrees to complete a project for a fixed price.
Individual Contracts: Each contract is a separate cost unit, and costs are tracked individually.
Direct Costs: These include materials, labor, and expenses directly related to the contracts. Indirect costs are also allocated based on contract size or duration.
Work-in-Progress: Since contracts are long-term, work-in-progress needs to be carefully measured at the end of each accounting period.
Recognition of Revenue: Revenue and profits are recognized based on the project's completion stage, often using the percentage of completion method.
Retention and Escalation Clauses: Contracts may include retention money (held until completion) and escalation clauses to account for cost changes.
Cost Control: Cost control involves monitoring costs against the contract's value to ensure profitability and efficient resource use.
Types of Contract Costing
Fixed Price Contract: In this type of contract, the contractor agrees to finish the project for a set price, regardless of the actual costs. The contractor bears the risk of cost overruns. For example, a construction company might agree to build a warehouse for a fixed price of 500,000.
Contract with Escalation Clause: This type of contract allows the price to be adjusted if certain costs, like materials or labor, increase. This reduces the contractor's risk due to price changes. For instance, a road-building contract might include an escalation clause that adjusts the price based on changes in asphalt costs.
Cost-Plus Contracts: In this contract, the contractor is paid back for allowed costs plus an extra amount for profit. This type of contract is useful when the project's scope is not well-defined. An example is a research project where the contractor is paid for all costs plus a percentage of these costs as profit.
Advantages of Contract Costing
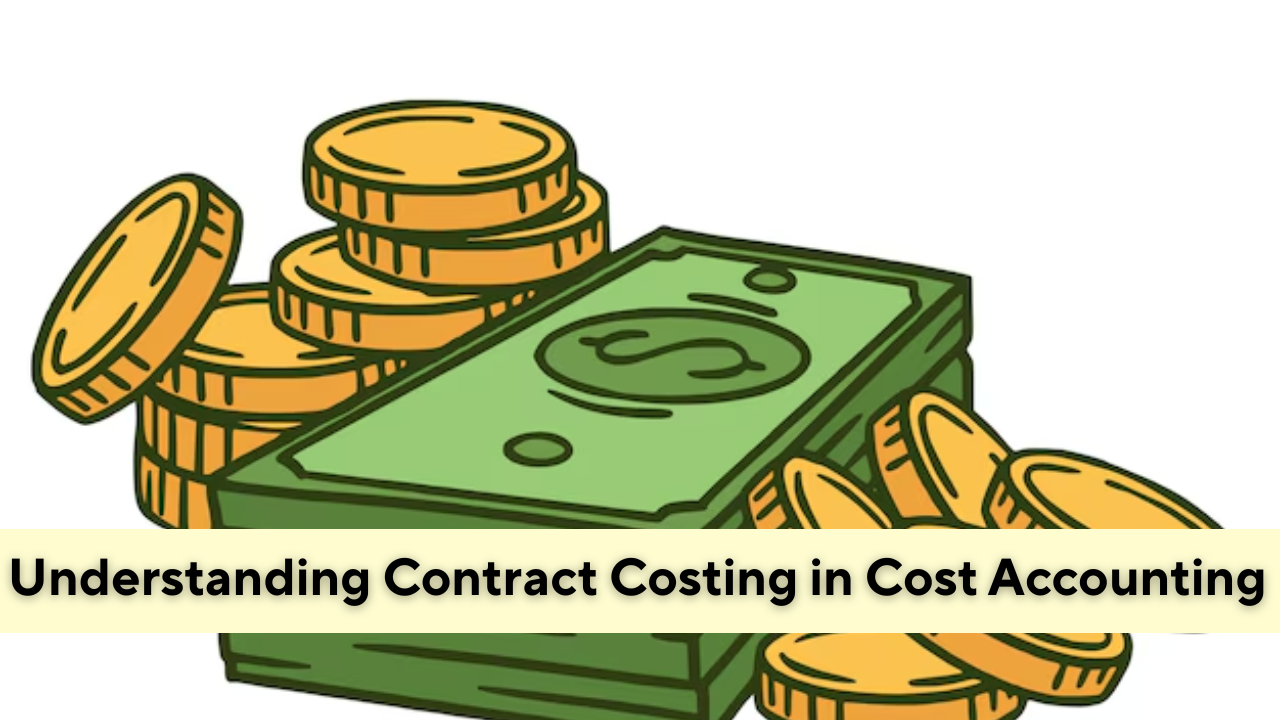
Given below are some of the Advantages of the contract costing:
Accurate Cost Tracking and Control
One of the main benefits of contract costing is the ability to track and control costs accurately for each contract. Since each contract is treated separately, all expenses for materials, labor, and overhead can be assigned and monitored precisely. This helps identify cost overruns and manage budgets more effectively.
Enhanced Cash Flow Management
Contract costing involves progress billing, where clients are billed at different project stages based on work completed. This ensures a steady cash flow throughout the project, crucial for maintaining liquidity, especially in long-term projects. It helps finance ongoing costs without relying solely on external funding.
Effective Profit Recognition and Reporting
Recognizing profits based on the percentage of completion provides a realistic view of a contract's financial progress. This approach aligns profit recognition with work done, offering an accurate picture of a company's financial health at any point. It's beneficial in long-term contracts where recognizing profit only at the end would distort financial results.
Risk Management through Retention Money and Escalation Clauses
Contract costing includes mechanisms like retention money (held until completion) and escalation clauses (to account for cost increases). These features help mitigate risks associated with non-performance, cost overruns, or inflation, protecting both the contractor and client.
Improved Decision Making
With detailed and accurate cost information, managers can make better decisions about resource allocation, pricing strategies, and contract terms. This level of detail aids in future contract negotiations and assessing new contract profitability.
Client Relationship and Satisfaction
Regular billing and certification of work done builds trust with clients, ensuring transparency in billing and work progress. This improves client relationships and satisfaction.
Efficiency in Long-Term Projects
Contract costing provides a structured approach to financial management for long-term projects. This approach ensures costs, timelines, and quality standards are adhered to, maintaining efficiency and effectiveness throughout the project lifecycle.
Features of Contract Costing
Given below are the highlights of the features of contract costing:
Then, after carefully including the client's requirements, a contract is drawn. Therefore, it is highly unlikely that any of these contracts would be similar.
Each of these contacts is a distinct cost unit to accumulate costs.
The structure of a cost contract states that there are more direct expenditures in the form of materials, wages and usage of stores or plants. Here, only a minimum charge is applicable for appointed overheads.
Contracts are for a longer period, typically more than a year.
The work is done at the site because it is difficult to exercise cost control.
Each contract has separate accounts to determine profitability.
Every contract work that involves construction must be done at the customer's site and not on factory premises.
Objectives of Contract Costing
Here are the objectives of Contract Costing mentioned below:
To determine the actual cost of each contract: The primary objective of contract costing is to determine the actual cost of producing goods or services under a specific contract. This involves identifying and accumulating all the direct and indirect costs associated with the contract.
To determine the profitability of each contract: Contract costing is used to determine the profitability of each contract. By comparing the actual cost of the contract to the estimated cost, management can determine whether the contract was profitable or not.
To determine the progress of each contract: Contract costing involves dividing the cost of each contract into stages or phases. This allows management to monitor the progress of the contract and to identify and any issues or delays that may impact the completion of the project.
To prepare accurate invoices: The cost of each contract is recorded and accumulated against each stage or phase. This information is used to prepare accurate invoices for the customer, based on the work completed and the cost incurred to date.
To improve cost control: Contract costing provides management with detailed information about the costs associated with each contract. This allows them to identify areas where costs can be reduced and to improve cost control in future contracts.
Difference Between Contract Costing and Job Costing
Scope: Job costing is for small, individual projects; contract costing is for large, long-term contracts.
Industries: Job costing is common in manufacturing and services; contract costing is prevalent in construction and engineering.
Duration: Job costing suits short-term projects; contract costing covers extended periods, often years.
Cost Tracking: Job costing tracks costs per job; contract costing tracks cumulative costs over the contract's duration.
Billing: Job costing typically bills upon job completion; contract costing often involves progress billing over the contract term.
Profit Recognition: Profit in job costing is recognized per job; contract costing is recognized over the contract's life, usually based on completion percentage.
Cost Fluctuation Risk: Job costing is less risky due to its shorter duration, while contract costing is more risky due to its longer timelines.
Overhead Allocation: Job costing involves directly allocating jobs; contract costing allocates overheads over the entire contract period.
Frequently Asked Questions
Q. What is contract costing when it is considered appropriate?
Contract costing is a cost accounting method used for tracking the expenses of individual, large-scale projects, especially in industries like construction and engineering. It's considered appropriate when projects are undertaken on a contract basis, typically requiring long-term site-specific work. Each contract is treated as a unique cost unit, with costs and revenues tracked separately.
Q. How much does an option contract cost?
An options contract costs a premium, which is the price paid by the buyer to the seller for the right (but not the obligation) to buy or sell the underlying asset at a specified price (strike price) and date (expiration date). Each contract usually represents 100 shares of the underlying security. The price of an option premium is determined by various factors, including the underlying asset's price, the strike price, the time until expiration, volatility, risk-free interest rates, and dividend rates.
Q. What is notional profit in contract costing?
Simply put, notional profit is an estimate of the potential profits that could be earned from a specific contract. It is a calculated figure used in contract costing formulas to help businesses determine the true cost of a project and decide whether or not to pursue it.
Q. How much does a futures contract cost?
A futures contract's cost is not a fixed price, but rather the price of the underlying asset at a future date, adjusted for factors like interest and time. The contract's value is determined by multiplying the contract size by the current market price. For example, a gold futures contract might represent 100 troy ounces of gold, and the price would be the current spot price of gold multiplied by 100.
Q. What are the key components of contract costing?
Contract costing, a specific type of job costing, has several key components including direct costs like materials and labor, indirect costs like overheads, and the allocation of costs to specific contracts. It also involves determining profit or loss on contracts, and may include features like escalation clauses and payments in installments.
Q. What is the work-in-progress (WIP) account in contract costing?
A Work-in-Progress (WIP) account represents the value of work completed on a contract that has not yet been billed to the client. It's essentially an asset on the balance sheet, reflecting the costs incurred for partially completed work on a long-term project. This account helps track the progress of a contract and the associated costs and revenue.
Q. How is profit calculated in contract costing?
In contract costing, profit calculation involves estimating total profit on incomplete contracts and recognizing a portion of that profit in the Profit and Loss Account. The process typically involves calculating notional profit, estimating total profit, and then transferring a portion of the estimated total profit to the Profit and Loss Account based on the degree of completion and cash received.