Top Six Sigma Interview Questions and Answers
Fri Apr 04 2025Are you preparing for a job interview that requires Six Sigma knowledge? Then you are at the right place. Multiple questions regarding six sigma Interview questions will appear in most interview sessions to evaluate your knowledge about this method. This guide presents a complete breakdown of the typical interview questions employers use for six sigma methodology with extensive explanations to support your interview success.
đŒA Brief About Six Sigma Interviews
Six Sigma functions as a significant organizational framework that many industries, including both manufacturing and healthcare services together with other domains, utilize. Organisations seek candidates who can effectively implement these principles in order to optimize process performance while reducing defects. Knowledge about six sigma interview questions determines whether you will secure your desired position or not.
Organizations must not underestimate Six Sigma's significance when operating in a competitive present-day business environment. Organisations across the world use data-driven processes to reduce both defects and process variations. Employers value candidates who comprehend Six Sigma fundamentals because they demonstrate their capability to boost the organizational excellence process.
đ€Question 1: What is Six Sigma and why is it important?
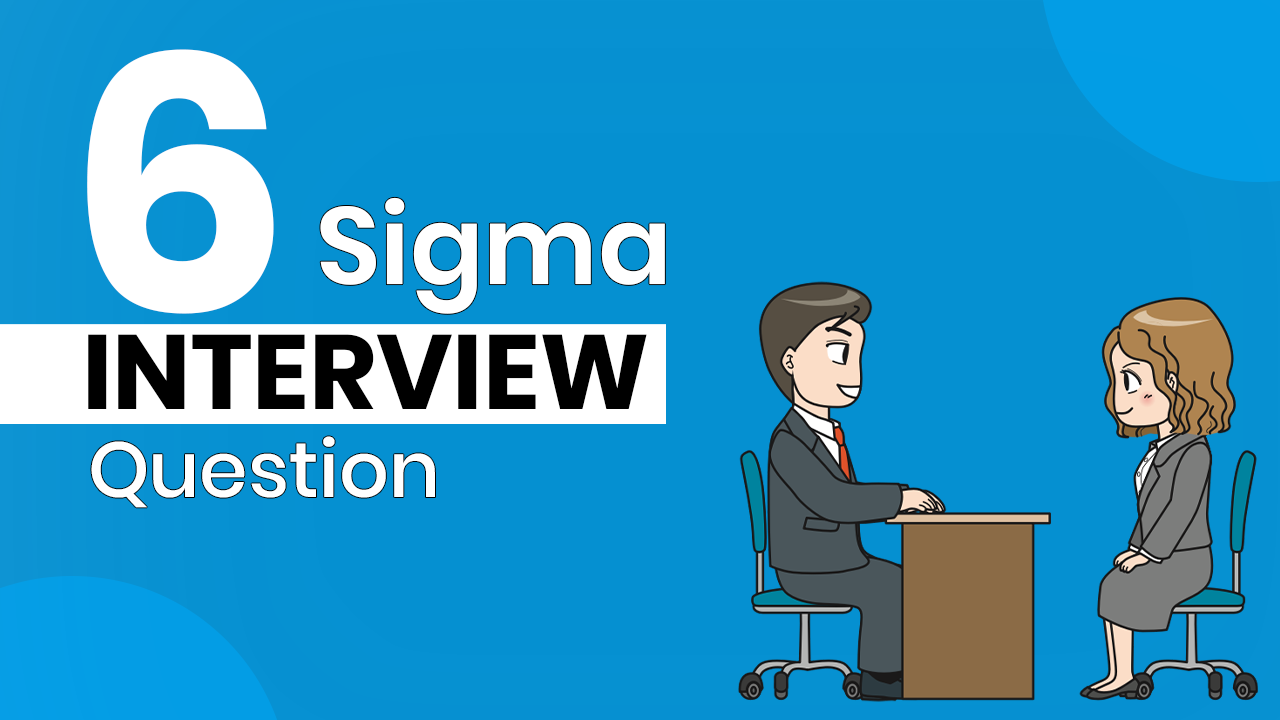
Sample Answer: "Six Sigma represents a structured approach based on analytical methods which aims to remove product errors while decreasing process inconsistency in business processes. The term âSix Sigmaâ describes a performance standard which allows 3.4 defects to exist within one million opportunities.
The importance of Six Sigma lies in its systematic approach to improving processes. It helps organizations:
Reduce operational costs
Increase customer satisfaction
Improve product quality
Enhance employee morale
Drive continuous improvement
Organisations deploy Six Sigma to generate quantifiable financial benefits and establish better operations combined with trained employees."
đQuestion 2: Explain the different types of Six Sigma methodologies.
Sample Answer: "There are several types of Six Sigma methodologies, each designed for specific improvement scenarios:
DMAIC (Define, Measure, Analyze, Improve, Control): This is the standard Six Sigma methodology used to improve existing processes that fall below specifications.
DMADV (Define, Measure, Analyze, Design, Verify): Also known as DFSS (Design For Six Sigma), this methodology is used when creating new processes or products.
IDOV (Identify, Design, Optimize, Validate): Another version of DFSS focused on product development.
DMEDI (Define, Measure, Explore, Develop, Implement): An alternative to DMADV, also used for creating new processes.
Lean Six Sigma: A combination of Lean principles (which focus on eliminating waste) and Six Sigma methods (which address variation).
Each methodology follows a structured approach to achieve specific goals, but DMAIC and DMADV are the most commonly used."
đQuestion 3: What is 6 sigma in terms of quality?
Sample Answer: "The 6 sigma measurement indicates an exceptional standard of quality performance. The definition of 6 sigma quality implies a process performance achieving 3.4 defects per million opportunities (DPMO). To put this in perspective:
3 Sigma = 66,807 DPMO (93.3% yield)
4 Sigma = 6,210 DPMO (99.38% yield)
5 Sigma = 233 DPMO (99.977% yield)
6 Sigma = 3.4 DPMO (99.9997% yield)
What is 6 sigma in quality? Essentially, it represents near-perfect quality. Processing at the 6 sigma level reaches such stability and capability that defects become very scarce. At this exceptional standard of quality businesses achieve better customer satisfaction while lowering their expenses and enhancing their organizational performance.
The achievement of this quality standard requires organizations to establish strict process control systems and continuous improvement measures."
đQuestion 4: Which one of the following is the Six Sigma methodology?
Sample Answer: "If presented with options, the correct Six Sigma methodology is DMAIC, which stands for:
Define: Identify the problem, scope, goals, and customer requirements
Measure: Collect data on the current process performance
Analyze: Identify root causes of defects and problems
Improve: Implement solutions to address root causes
Control: Maintain the improvements by standardizing processes
The DMAIC approach serves as one of the Six Sigma methodologies since it stands as the traditional framework for implementing Six Sigma projects. DMAIC represents the core methodology people usually link to Six Sigma yet additional methodologies such as DMADV, IDOV, and DMEDI serve specific purposes."
đ§ Question 5: What concepts does Six Sigma include?
Sample Answer: "Six Sigma concept includes several key elements that work together to form a comprehensive improvement approach:
Statistical thinking and tools: Using data and statistical analysis to make decisions
Process focus: Understanding that all work occurs in processes that can be measured and improved
Voice of the Customer (VOC): Ensuring customer requirements drive improvement efforts
Variation reduction: Identifying and minimizing sources of variation in processes
Belt-based training system: Structured training approach (Yellow, Green, Black Belts, etc.)
Project-based implementation: Applying Six Sigma through specific improvement projects
DMAIC methodology: The systematic approach to problem-solving
Continuous improvement culture: Creating an organizational mindset focused on ongoing enhancement
Measurement systems: Ensuring accurate data collection and analysis
Process capability analysis: Evaluating how well processes meet specifications
Six Sigma concept includes these foundational elements that provide a framework for achieving breakthrough improvements in any business process."
â Question 6: What does a process that performs at a 6 sigma level mean?
Sample Answer: "A process that performs at a 6 sigma level means it has reached an extremely high standard of quality where only 3.4 defects occur per million opportunities. This represents a 99.9997% defect-free rate.
To understand this in practical terms:
If a hospital operated at a 3 sigma level, they would perform 5,000 incorrect surgical procedures per million
At a 6 sigma level, this would reduce to just 3.4 incorrect procedures per million
A process that performs at a 6 sigma level has several characteristics:
It's highly stable and predictable
It has minimal variation
It consistently meets or exceeds customer expectations
It requires less inspection and rework
It costs less to maintain than lower-performing processes
Achieving this level requires rigorous process control, robust measurement systems, and an ongoing commitment to improvement."
đAdditional Important Six Sigma Interview Questions
đ„What are the different Six Sigma belt levels and their roles?
Sample Answer: "Six Sigma uses a belt certification system similar to martial arts:
White Belt: Basic awareness of Six Sigma concepts
Yellow Belt: Understands basic tools and can participate in projects
Green Belt: Can lead small projects while maintaining regular job duties
Black Belt: Full-time improvement professional who leads complex projects
Master Black Belt: Coaches Black Belts and Green Belts, develops training materials
Champion: Executive who supports projects and removes organizational barriers
Each level requires specific training and project experience, with higher belts taking on more complex improvement challenges and leadership responsibilities."
âïžWhat is the difference between Lean and Six Sigma?
Sample Answer: "While both Lean and Six Sigma aim to improve processes, they have different focuses:
Lean:
Focuses on eliminating waste (anything that doesn't add value)
Aims to improve flow and reduce cycle time
Uses tools like Value Stream Mapping and 5S
Origins in Toyota Production System
Six Sigma:
Focuses on reducing variation and defects
Uses statistical tools to analyze problems
Follows DMAIC or DMADV methodologies
Origins at Motorola and General Electric
Many organizations now use Lean Six Sigma, which combines both approaches to eliminate waste while also reducing variation."
đŻHow do you select a Six Sigma project?
Sample Answer: "Selecting the right Six Sigma project is crucial for success. The best projects are:
Aligned with business goals: Projects should support organizational objectives
Measurable: Clear metrics must exist to track improvement
Manageable in scope: Projects should be completed in 3-6 months
Significant impact: Focus on issues causing substantial pain or cost
Data-driven: Sufficient data should exist or be collectible
Supported by leadership: Management must commit resources
A good selection process includes developing a project charter that defines the problem, scope, goals, team members, timeline, and expected benefits before work begins."
đ ïžWhat statistical tools are commonly used in Six Sigma?
Sample Answer: "Six Sigma relies on numerous statistical tools across the DMAIC phases:
Define phase: SIPOC diagrams, Voice of Customer tools, Project Charter
Measure phase: Process mapping, Measurement System Analysis (MSA), capability analysis
Analyze phase: Hypothesis testing, correlation analysis, regression analysis, ANOVA
Improve phase: Design of Experiments (DOE), FMEA (Failure Mode and Effects Analysis)
Control phase: Control charts, Statistical Process Control (SPC)
Pareto charts together with cause-and-effect diagrams and histograms represent other supplementary analytic tools. The selection process for tools depends on both the requirements of the project work and the characteristics of the analyzed data."
đHow would you explain Six Sigma to someone with no technical background?
Sample Answer: "I will describe Six Sigma as a methodology that discovers and repairs operational errors during the production phase before they occur. Baking cookies requires a specific process where you sometimes end up with products that are either stiff or mushy. Six Sigma provides the solution to uncover perfect cookie-making conditions which include temperature control and ingredient selection and baking duration.
The precise measurement of key elements combined with proper control enables you to generate perfect cookies repeatedly. Six Sigma delivers identical process management solutions to business operations by minimizing mistakes and waste to deliver steady high-quality products and services.
The statistical term '6 Sigma' signifies achieving such high levels of ability that you only make errors less than four times within one million attempts."
đŻConclusion
Knowledge of both theory and practical usage of Six Sigma methodologies is required to properly prepare for interview questions about this management system. Your preparation for Six Sigma interviews becomes successful when you learn the standard questions while developing purposeful answers which reveal your expertise.
Companies seek interview candidates who understand Six Sigma principles alongside their ability to put these principles to work on specific business issues. Multiple examples from your personal experience must accompany your responses whenever possible to prove your hands-on understanding.
The mastery of these interview questions will make you the ideal job candidate to both fresh and experienced Six Sigma practitioners who want to exhibit their worth to hiring organizations.
đ€Frequently Asked Questions
1. How do you explain Six Sigma in an interview?
Six Sigma is a data-driven methodology that improves processes by reducing defects and variations, enhancing efficiency and quality.Six Sigma is a data-driven methodology that improves processes by reducing defects and variations, enhancing efficiency and quality.
2. What is the full form of Six Sigma?
Six Sigma doesnât have a full form but refers to a set of techniques for process improvement, aiming for near-zero defects (3.4 defects per million).
3. What are the 5 elements of Six Sigma?
Define, Measure, Analyze, Improve, and Control (DMAIC) â the structured problem-solving approach in Six Sigma.
4. What is Six Sigmaâs main goal?
To reduce defects and process variations, improve quality, and enhance efficiency to achieve near-perfect performance.
5. What are the 6 points of Six Sigma?
Customer focus
Data-driven decision-making
Process improvement
Proactive management
Collaboration
Continuous improvement
6. What are the different Six Sigma belts?
White, Yellow, Green, Black, and Master Black Belt â each representing different levels of expertise in Six Sigma.
7. How is Six Sigma different from Lean?
Six Sigma focuses on reducing defects, while Lean aims to eliminate waste for process efficiency. Both are often used together.